IMPLEMENTATION OF SCADA SYSTEM FOR CONTROL AND MONITORING IN MARIWAD PUMP STATIONS
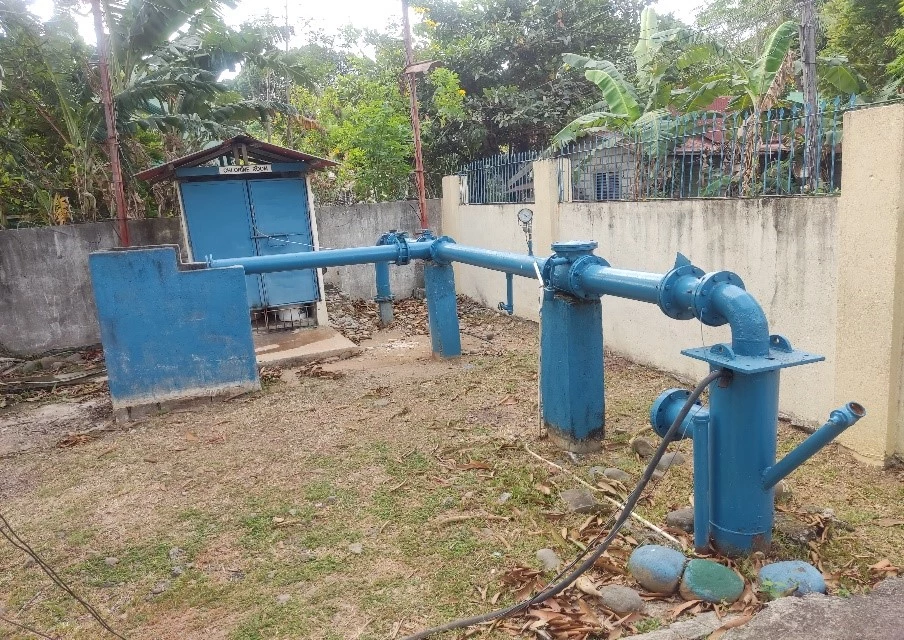
VTSCADA has comprehensive functionality, reliability, and flexibility, enable efficient monitoring, control, and management of critical water infrastructure.
To ensure the smooth operation of water pumping substations within a district.
A central monitoring station obtains real-time data on pump performance, water flow rates, pressure levels, and even energy consumption from sensors installed strategically throughout the substation.
Modernizing the power supply systems with energy-efficient motors, variable frequency drives (VFDs), and optimized load management reduces energy consumption and operating costs.
By providing a clear picture of substation activity, VTSCADA empowers water districts to enhance efficiency, minimize downtime, and ultimately deliver a reliable water supply to their consumers.
Benefits
Increased operational efficiency through automation and real-time monitoring.
Cost savings from energy-efficient systems and reduced maintenance.
Sustainable water resource management by preventing overuse of groundwater.
Improved reliability and safety through enhanced controls and predictive maintenance.
VTScada System UI For Single Monitoring
VTScada System UI For Multiple Monitoring